The recent NATO-Industry Forum in Stockholm was a high-level conference hosted by the NATO Secretary General. Discussions were dominated by the need for NATO nations to continue to stand full square behind Ukraine and provide their armed forces with the support they need. In remarkable government-military-industry alignment, the need for urgency was reinforced in what one senior person described as a combined NATO & Industry Call to Arms. Nations must expand production capacity, develop more resilient supply chains and work coherently across a plethora of initiatives and institutions in EU and NATO.
To make this happen, NATO has agreed a Defence Production Action Plan (DPAP). This commitment is just the latest in progressive recognition that we must pay more attention to operational availability, supportability and resilience of our systems and their supply chains.
Back in 2020, UK Chief of Defence Staff predicted in his annual speech to RUSI that what had worked for the predictability of stabilisation and counter insurgency operations over 20 years of war in Iraq and Afghanistan will no longer be sufficient. Before 1990, stock dispersal and holding war reserves were deemed essential. But since the end of the Cold War and the desire for Peace Dividends, nations have sought to reduce the cost of spare parts inventory. There has been a progressive shift since towards optimisation, centralisation, contingency stocks rather than war reserves in an incessant drive to reduce cost. Years of efficiency initiatives have taken risk against readiness and resilience as the optimised logistic infrastructure, reduced inventory, rationalised stock, and outsourced much work to industry. Indeed, the extra cost of 2 Gulf Wars and Afghanistan was met by government contingency funding rather than normal budgets.
CDS remarked that nations must be honest about the true state of our forces and how we mobilise ourselves to improve readiness and enhance resilience. He raised some pertinent questions about lessons to learn to fight the next war:
- Do we know what just-in-time logistics has done to our supply chains?
- Have we assured sovereign capability where needed?
- Has competitive procurement shared risk for our support solutions worked with our suppliers as well as it should?
- How do we improve the availability of key platforms?
Both the Coronavirus pandemic and now the war in Ukraine have both confirmed CDS’ foresight. We must focus on resilience and restore stockpiles despite the previous financial anathema. But we must not just engage in a spending spree as we still need to spend taxpayers money wisely. How can that be achieved?
Resilience and Supportability
Resilience can be defined as the capacity to recover quickly from difficulties – to spring back into shape. For many years, resilience has been synonymous with large spare parts inventory but, in practice, is more complex with multiple factors.
TFD defines Supportability as the responsiveness to unreliability that prevents a system’s use. In other words, ‘when there’s a problem on a system, how quickly can its utility be restored’. Resilience.
Enhanced stockpiles will contribute to Resilience but there are 2 other critical factors.
- First, spare parts alone are insufficient. Reserves of skilled people, tools, test equipment, deployed facilities and rapid access to information are also essential.
- Second, a lesson from Iraq and Afghanistan was the need to speed up the repair of critical items. Huge amounts of new equipment were shipped into theatre but far fewer returned for repair. After some years, forward repair capabilities were created to cut down repair time delays.
Improve System Supportability
Supportability of a system can be measured directly as the sum of all system Downtime for preventative, corrective maintenance and condition-based monitoring, and Administrative & Logistic Delay Time (ALDT). Supportability can be measured as a simple single metric both for each component in the ranked histogram shown in the graphic below and the total area under the curve describes the overall system. Better system Supportability means less Downtime and more operational availability.
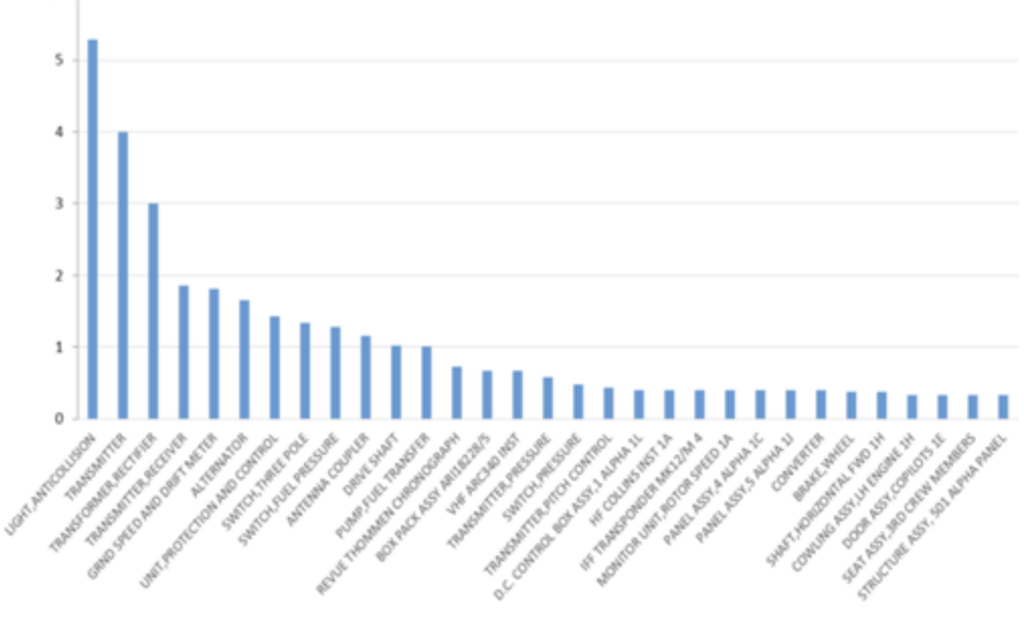
Although linked to availability and maintainability, Supportability is independent of reliability and cost. Improving reliability does not make a system more Supportable. Reduced failure rates will reduce the cost and may reduce planned maintenance burdens but not inevitably. Additional stock helps but does not, on its own, make a system more Supportable bit is dependent on having all the necessary resources immediately to hand – people, tools, support equipment, information as well as spares. Holistic Supportability management is needed to identify the most important and cost-effective Resilience improvements for both peace and war.
TFD’s Supportability Audit technique of current systems can identify how to identify potential issues areas for improvement and drive down delay time, improve operational availability and Resilience.
The important outcome is not to create vast Happy Shelves of spare parts in theatre but more available Happy Systems through improved Supportability delivered by affordable effective logistics footprints at home, in transit and deployed.
Dynamically Improve Repair Times
Rapid repair directly enhances Support Advantage by reducing logistic drag and downtime. Applied to critical, typically complex and expensive items, this can have a very significant impact. Overall fill rates can be increased relatively cheaply with large stocks of consumables such as nuts, bolts and washers, but operational availability is normally constrained by shortage of the more expensive LRUs. Stock levels are determined by the number of failures expected during the planned repair turn round time to keep the pipeline full.
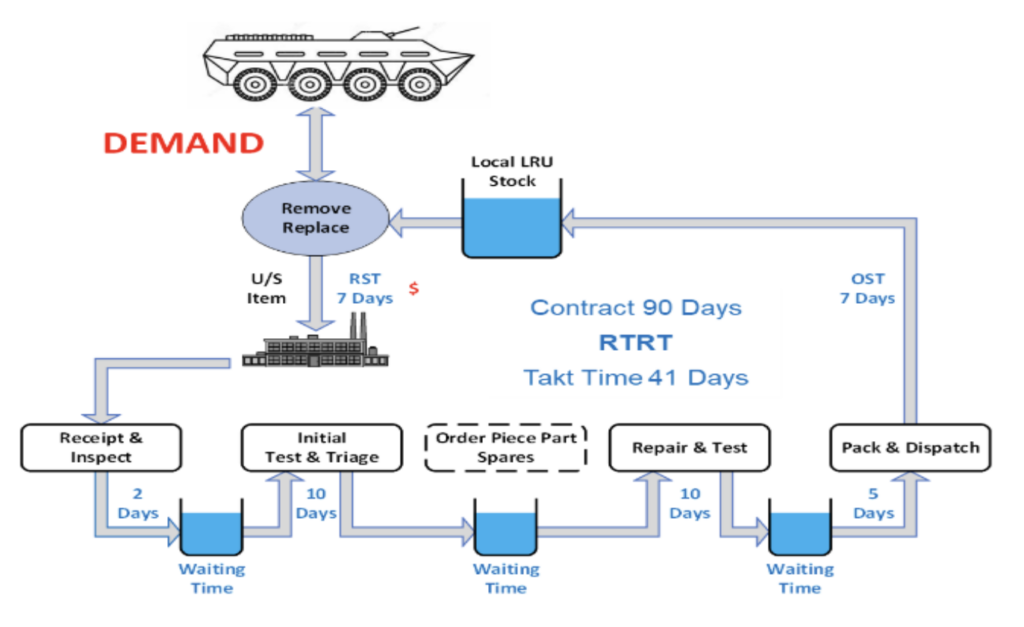
Repair contracts can be structured in many ways but the most common is for fixed repair turnround times (RTRTs) such as 90 days. Actual ‘spanner in hand’ (TAKT) time for repairs will be less, perhaps only 30 days, so much time is spent awaiting work. This approach de-risks contractors’ delivery timescales and allows various repair prioritisation strategies such as Fixed RTRT, First-In First-Out, profit maximisation (expensive items that generate most profit are worked first) or in whatever order the repair manager prefers. In all cases, items are held back until contractually required which reduces stock available at units constraining Ao. These strategies preserve Happy Shelves and are not aimed at Happy Systems.
TFD have developed an ensemble AI technique which dynamically prioritises repairs based on projected future demand. Unlike other AI solutions, it also accommodates seemingly unpredictable demands for random corrective maintenance. Think of the order number screens in MacDonalds which determine what is cooked and in what order.
In data experiments, system availability increased by 11% for an optimised spares solution merely by repairing items in a dynamic order without any increase in spares investment. Indeed, the AI will automatically slow down induction of items with excess stock in cost-saving repair holidays. For sub-optimal stock holdings, the increase in availability is even greater at circa 20%. The dynamic AI reacts faster than humans to detect and manage increases in arising rates from emergent engineering issues as shown below. Similarly, it will automatically react to operational surges for deployments and conflict. Lastly, if repair prioritisation is assumed to be available from the outset, initial provisioning costs could be reduced very significantly with no operational impact.

The Repair Induction Prioritisation Engine (RIPE) improves system availability in many cases at no more and often less cost. The approach would greatly improve system availability during conflict for no additional investment and make a major contribution to delivering Support Advantage.
‘The ability of UK Defence to deter and, if necessary, out-compete its near-peer enemies by our key capabilities being more available, more of the time, where and when we need them, and possessing support chains which are more resilient than those who oppose us.
For more information about all
TFD products please contact:
Email: allan.goody@tfdg.com
Tel: +44 (0) 1603 726660